Project Paper Weight
This is a stock to current description of how I managed to turn my truck into something even I have difficulty acknowledging the usefulness of.
The Beginning
As purchased, June 03. Only picture I have, wish I had been more judicious in capturing some pics.
The first round of mods were tame, I knew it was going to be driven a lot and I didn't have the money to regear. It ended up with a 6" Superlift kit and some 15x10 steelies wrapped in 33" BFG A/T's. The bumper and winch were already on the truck.
I threw on some nerf bars which were bent and crushed in short order.
Sometime here I bought a used Can-Bak so I could camp in the truck and being my complete lack of skill with metal hired Mr. Payne to build me some sliders.
As we were fitting and he was welding them on.
Shortly thereafter I did a shackle flip that Jason sold to me off the cutoff section of his trucks frame and put on some Realift t-bar drop eliminators, which resulted in the situation above. T-bars stripped out the stacked plate adapters and left it on the bump stops, had to call my dad to come pick the truck up. Up to this point I'd been putting front end parts into the truck entirely too regularly. I think I was on the 6th ball joint, 4th TRE, 3rd hub, and everything else once. Jason helped me come up with a solution.
This is a stock to current description of how I managed to turn my truck into something even I have difficulty acknowledging the usefulness of.
The Beginning
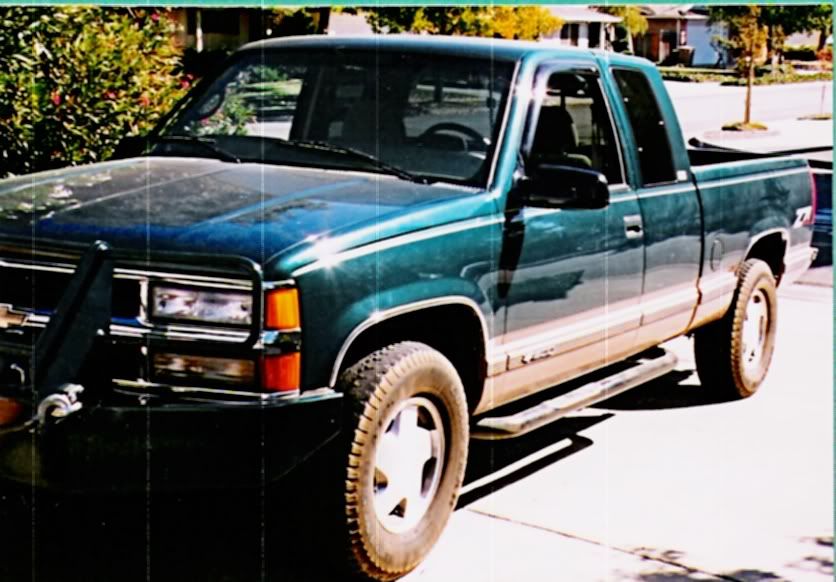
As purchased, June 03. Only picture I have, wish I had been more judicious in capturing some pics.
The first round of mods were tame, I knew it was going to be driven a lot and I didn't have the money to regear. It ended up with a 6" Superlift kit and some 15x10 steelies wrapped in 33" BFG A/T's. The bumper and winch were already on the truck.
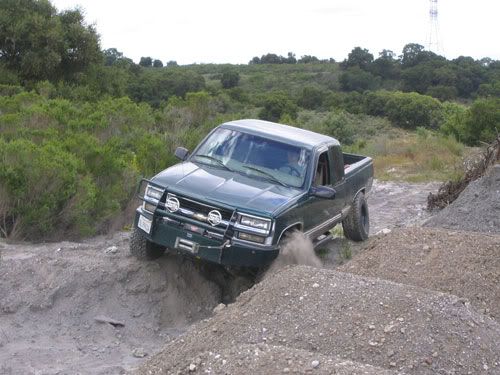
I threw on some nerf bars which were bent and crushed in short order.
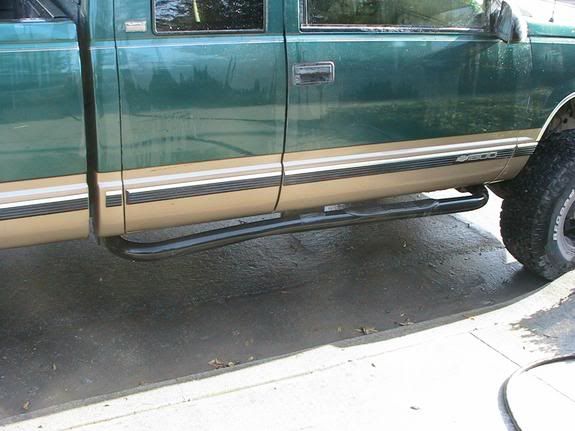
Sometime here I bought a used Can-Bak so I could camp in the truck and being my complete lack of skill with metal hired Mr. Payne to build me some sliders.
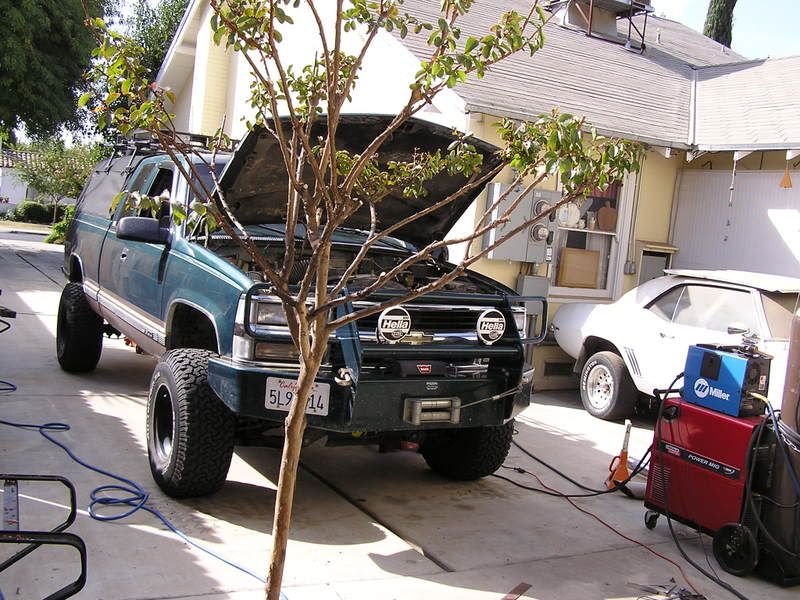
As we were fitting and he was welding them on.
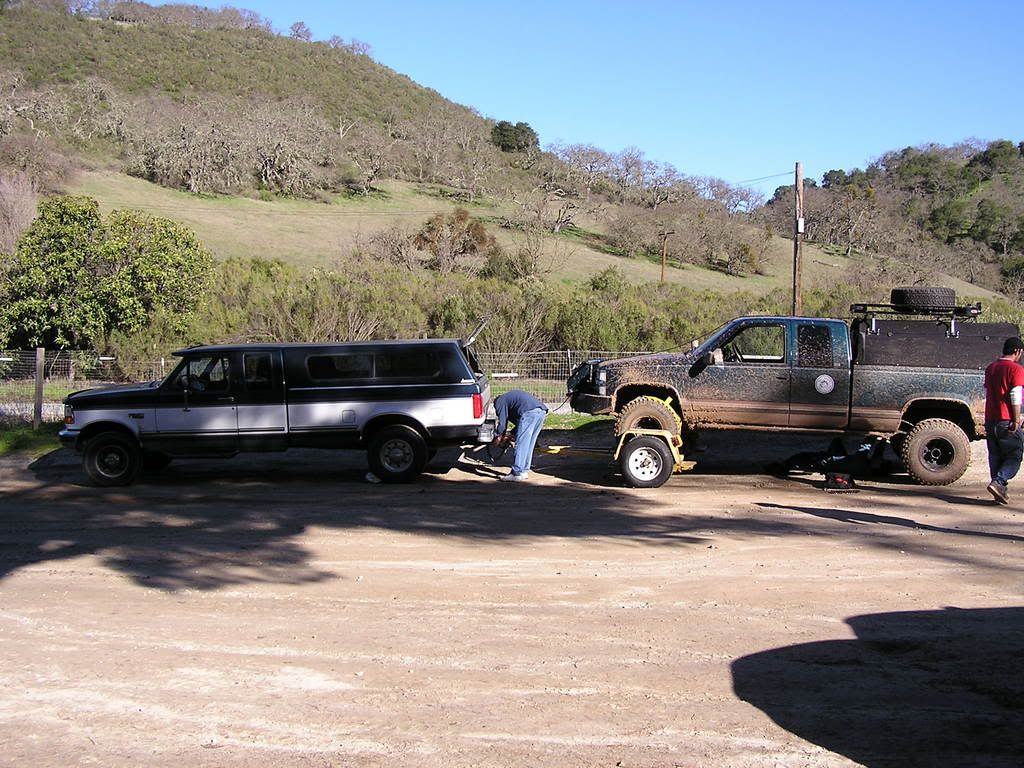
Shortly thereafter I did a shackle flip that Jason sold to me off the cutoff section of his trucks frame and put on some Realift t-bar drop eliminators, which resulted in the situation above. T-bars stripped out the stacked plate adapters and left it on the bump stops, had to call my dad to come pick the truck up. Up to this point I'd been putting front end parts into the truck entirely too regularly. I think I was on the 6th ball joint, 4th TRE, 3rd hub, and everything else once. Jason helped me come up with a solution.